To download the documents you need to have a valid username and password.
To receive your registration data, please contact us on +49 7371 9508-0.
EWA 50
- EWA 50 - 230V 1~ We06
- EWA 50 - 230V 1~ We66
- EWA 50 - 230V 1~ We06 (shaft height 60 mm)
- EWA 50 - 230V 1~ We66 (shaft height 60 mm)
- EWA 50 - 400V 208V 480V 3~ We06
- EWA 50 - 400V 208V 480V 3~ We66
- EWA 50 - 400V 208V 480V 3~ We06 (shaft height 60 mm)
- EWA 50 - 400V 208V 480V 3~ We66 (shaft height 60 mm)
- EWA 50 - 120V 240V 1~ We06
- EWA 50 - 120V 240V 1~ We66
- EWA 50 - 120V 240V 1~ We06 (shaft height 60 mm)
- EWA 50 - 120V 240V 1~ We66 (shaft height 60 mm)
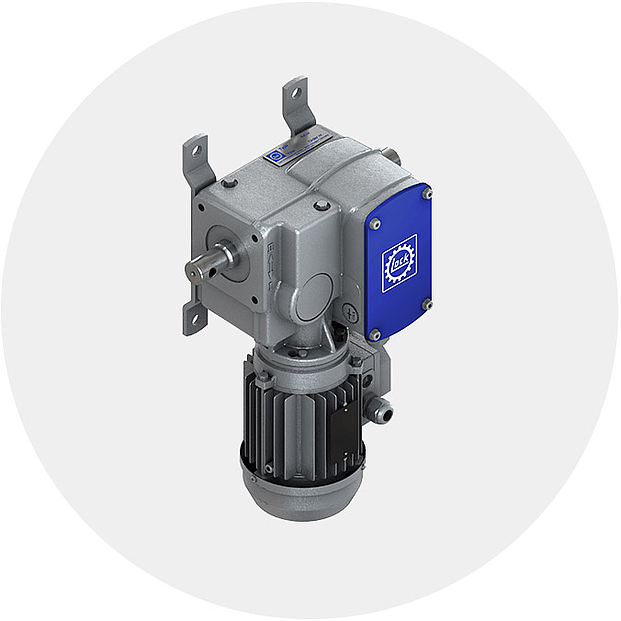
EWA 10
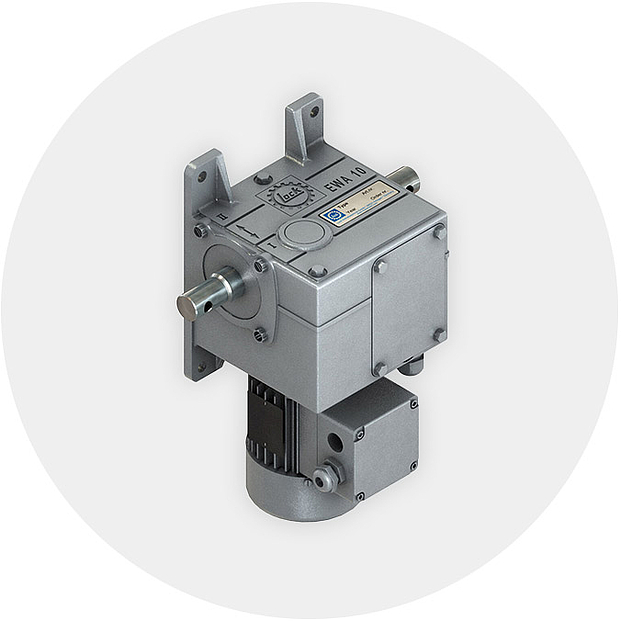
EWA 12
- EWA 12 - 24V We06
- EWA 12 - 120V We 06
- EWA 12 - 208V We 06
- EWA 12 - 230V We 06
- EWA 12 - 230V We 66
- EWA 12 - 240V We 06
- EWA 12 - 400V We 06
- EWA 12 - 400V We 66
- EWA 12 - 480V We 06
- EWA 12 - 120V We 06 (shaft height 60 mm)
- EWA 12 - 208V We 06 (shaft height 60 mm)
- EWA 12 - 230V We 06 (shaft height 60 mm)
- EWA 12 - 230V We 66 (shaft height 60 mm)
- EWA 12 - 240V We 06 (shaft height 60 mm)
- EWA 12 - 480V We 06 (shaft height 60 mm)
- EWA 12 - SPL 30 We 06
- EWA 12 - SPL 30 We 66
- EWA 12 - 24V We06
- EWA 12 - 120V We 06
- EWA 12 - 208V We 06
- EWA 12 - 230V We 06
- EWA 12 - 230V We 66
- EWA 12 - 240V We 06
- EWA 12 - 400V We 06
- EWA 12 - 400V We 66
- EWA 12 - 480V We 06
- EWA 12 - 120V We 06 (shaft height 60 mm)
- EWA 12 - 208V We 06 (shaft height 60 mm)
- EWA 12 - 230V We 06 (shaft height 60 mm)
- EWA 12 - 230V We 66 (shaft height 60 mm)
- EWA 12 - 240V We 06 (shaft height 60 mm)
- EWA 12 - 480V We 06 (shaft height 60 mm)
- EWA 12 - SPL 30 We 06
- EWA 12 - SPL 30 We 66
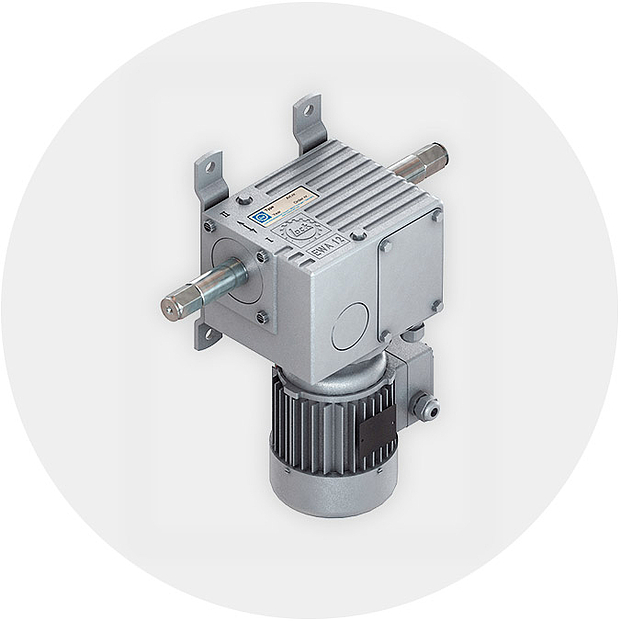
EWA 14
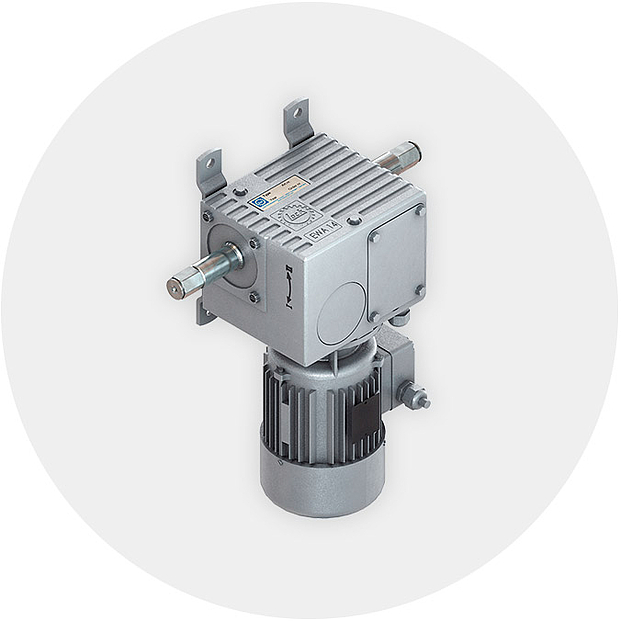
EWA 16
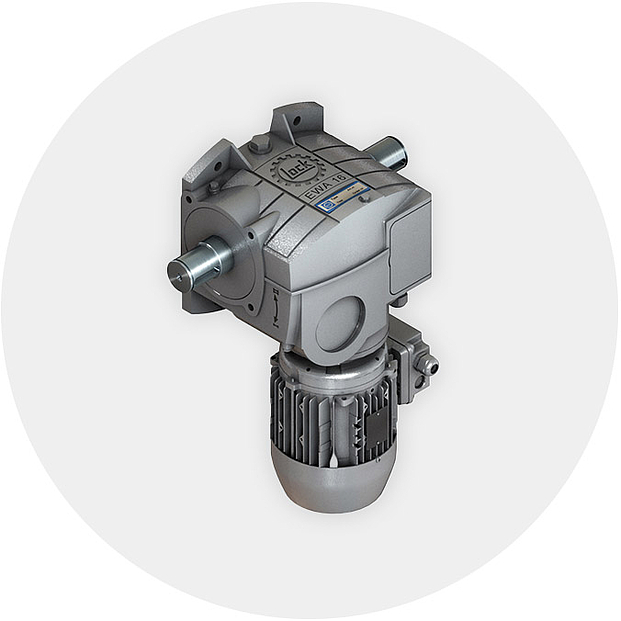
EZW 64
EZW 64 - Basic
- EZW 64 - Basic 230V 5000N
- EZW 64 - Basic 230V 10000N
- EZW 64 - Basic 230V 20000N
- EZW 64 - Basic 400V 5000N
- EZW 64 - Basic 400V 10000N
- EZW 64 - Basic 400V 20000N
EZW 64 - Swing
- EZW 64 - Swing 230V 5000N
- EZW 64 - Swing 230V 10000N
- EZW 64 - Swing 230V 20000N
- EZW 64 - Swing 400V 5000N
- EZW 64 - Swing 400V 10000N
- EZW 64 - Swing 400V 20000N
EZW 64 - Swing Lagerbock
Zahnstangen
- EZZ 64 5000N - EZZ 64.05606
- EZZ 64 5000N - EZZ 64.05608
- EZZ 64 5000N - EZZ 64.05610
- EZZ 64 5000N - EZZ 64.05612
- EZZ 64 10000N - EZZ 64.1006
- EZZ 64 10000N - EZZ 64.1008
- EZZ 64 10000N - EZZ 64.1010
- EZZ 64 10000N - EZZ 64.1012
- EZZ 64 20000N - EZZ 64.2006
- EZZ 64 20000N - EZZ 64.2008
- EZZ 64 20000N - EZZ 64.2010
- EZZ 64 20000N - EZZ 64.2012
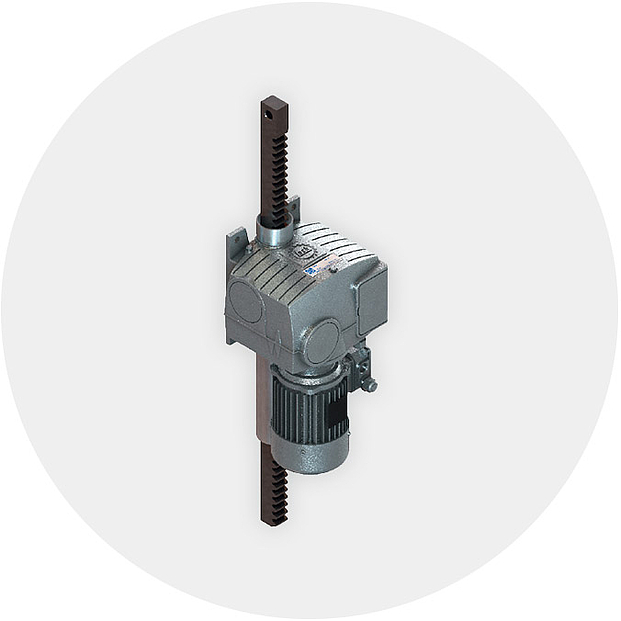